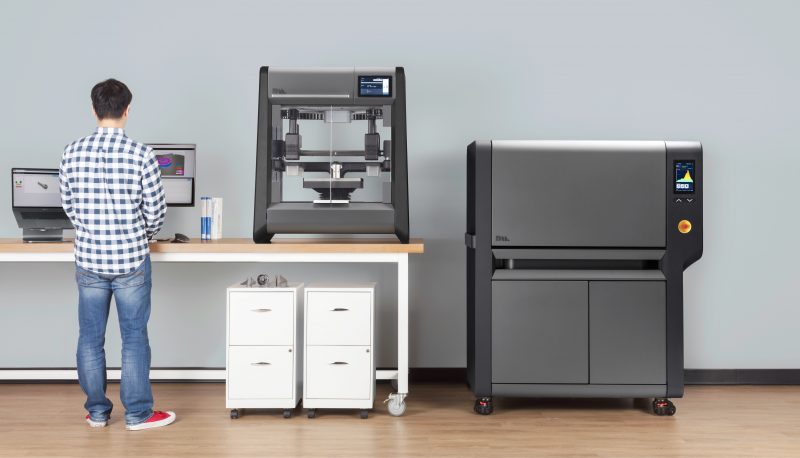
Studio System. From left to right: Console, Printer and, Furnace. (Credit: Desktop Metal)
Sometimes the hype before the reality is well founded. Burlington, Mass. company Desktop Metal, is preparing to revolutionize manufacturing with 3D metal printing systems that address the unfulfilled challenges of speed, cost, and quality. Metal 3D printing, often referred to as additive manufacturing, has failed to deliver on the expectation that it would dramatically change the way products are manufactured. For now, practically all 3D printing is done with cheap plastic extrusion materials, because 3D printing with laser-melted metal printing, is very expensive and slow. However, the latest market intelligence report from IDTechEx Research, 3D Printing Metals 2018-2028: Technology and Market Analysis projects that metal printer manufacturers and materials suppliers are going to grow 3D metal printing into a $12B market by 2028.
Desktop Metal (DM) is bringing to market two systems: a studio system called DM Studio System targeting engineering groups, offering rapid, relatively inexpensive metal prototyping and a production system called DM Production System for mass manufacture.
Desktop Metal’s Studio System as mentioned is meant for rapid prototyping, built on a cloud-based software architecture, that allows an engineer to go immediately from CAD 3-D model to part production. The target market for this product is mechanical engineers using it for prototyping and printing a small number of parts at corporate offices rather than factories. The metals for the system come in rod form, instead of hazardous, volatile metal powders used in commercial laser-based additive systems. The wide range of metals that DM offers are melted by a user-friendly sintering furnace that reaches a top temperature of 1400º C. The DM Studio System was designed to provide an automated and managed workflow controlled and monitored from the cloud, by sophisticated software. Studio System begins shipping this year, starting at $120,000 and is 10 times cheaper than modern laser-based additive systems.
The DM Production System uses a new technology called Single Pass Jetting, to build metal parts 100x faster (up to 500 cubic inches per hour) and up to 20 times less expensive at a still hefty price of $360,000, than today’s fastest metal, laser-based additive systems. Material costs will also be up to 20 times lower, as they use regular, low-cost, easily available MIM powders
Video Transcript: